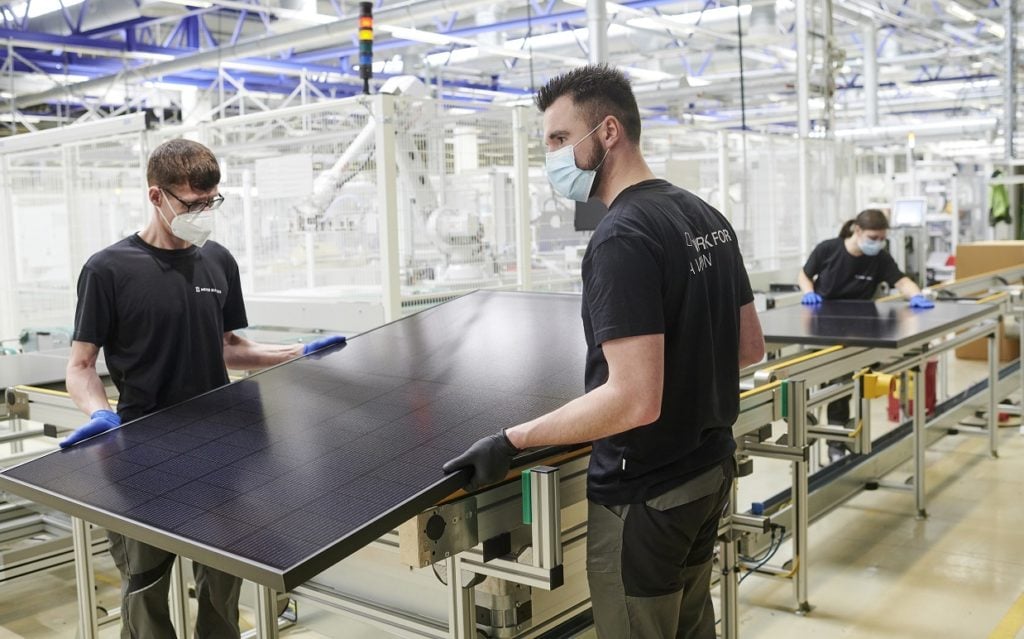
Leading solar manufacturers have implored governments to implement tax credits and other financial incentives to stimulate domestic PV manufacturing.
Officials from Qcells, Canadian Solar and JinkoSolar have discussed the subject in recent weeks, highlighting a perceived need for the financial case for solar manufacturing to be propped up with tax breaks and other incentives in order for PV manufacturing bases to compete with China.
However that opinion is not shared universally, with many in the space concluding that if sufficient scale can be achieved, regional manufacturing could compete on a cost basis with China, with access to finance being the last remaining hurdle.
Earlier this week, during the firm’s Q1 2022 results disclosure, Canadian Solar chief executive Shawn Qu was asked by analysts if the company was considering expanding its manufacturing footprint outside of China and Southeast Asia given the much-documented issues affecting the supply of solar modules to the country.
Canadian Solar had outlined plans to invest US$850 million in a capacity expansion plan, ramping up solar ingot, wafer and cell manufacturing capacity in a bid to reduce its exposure to pricing volatility, however all of this new capacity is to be based in China and Thailand.
Qu told analysts that tariffs alone would not be enough to “force manufacturers into the US”.
“Some good, long-lasting local incentives would attract capacity into the US,” Qu said, alluding to the proposed Solar Energy Manufacturing for America (SEMA) Act proposed last year by Senator Jon Ossoff and included within President Joe Biden’s Build Back Better agenda.
That view has been echoed by Qcells CEO Justin Lee, who in a press conference earlier this month said that direct subsidies for manufacturing were critical for more regionalised solar manufacturing.
“This industry clearly needs some kind of incentive or subsidy,” Lee said, adding that other regulatory levers, such as import tariffs or carbon footprint requirements, are “not good enough”.
Qcells recently unveiled plans to invest US$320 million to expand its solar cell and module manufacturing capacities in Korea and the US respectively, however the company remains enthused by the prospect of SEMA passing and providing direct incentives on a cost-per-unit basis for the manufacture of solar polysilicon, wafers, cells and modules in the US.
Ossoff’s SEMA bill has emerged as a particular favourite of solar manufacturers eyeing expansion plans given, as Lee noted, its cost-per-unit model. The initial proposals tabled last year include tax credits of US$3/kg for polysilicon, US$12/sqm of solar wafers, US$0.04/Wdc for solar cells and US$0.07/Wdc for non-integrated modules and US$0.11/Wdc for integrated modules.
“Some good, long-lasting local incentives would attract capacity into the US”
Shawn Qu, Canadian Solar
“From the cost perspective [outlined in Senator Jon Ossoff’s SEMA proposal], we are satisfied. If that policy support is in place, we may consider [expanding in the US],” he says.
Lee’s full sentiments regarding Qcells’ expansion plans can be read here.
Qcells parent company Hanwha Solutions has, of course, already committed to a broader restart of a solar manufacturing landscape in the US, starting with the purchase of a significant stake in polysilicon producer REC Silicon and a commitment to restart production at the Moses Lake facility REC mothballed in 2019.
But while the SEMA bill has been championed by solar manufacturers – and, in a similar fashion, India’s Production Linked Incentive scheme has also been successful in attracting gigawatts of interest – Europe has offered no such fiscal incentive for solar manufacturers, instead choosing to address issues relating to the availability of finance.
Last week’s Solar Strategy, published as part of the European Commission’s REPowerEU plan, established initiatives such as a continued investment in solar R&D through the EU’s Horizon programme and the launch of the EU Solar PV Industry Alliance which will bring together stakeholders to tackle common issues and grow the use of existing financing mechanisms, such as the EU Innovation Fund and InvestEU, which would support financing of PV manufacturing.
The absence of pure incentives like those seen in the US and India could be a factor for manufacturers considering where to expand production.
Speaking to PV Tech at this month’s Intersolar Europe event, Frank Niendorf, general manager for Europe at JinkoSolar, said that while the manufacturer, which has had some regional manufacturing in Portugal, South Africa and the US, albeit on a small scale, would consider localised facilities if there was no other way of servicing particular markets.
But, Niendorf said, customers would have to be aware of the cost involved.
“If we did such an investment in Europe again, which I would not completely rule out if the political decision making and the industrial coalitions in Brussels lead into that direction, it would lead to a significant price increase for the modules, and that’s something which has to be carefully taken into account,” Niendorf said.
Other manufacturers would, however, disagree. At this month’s Intersolar Europe Dr Peter Fath of Turkish PV manufacturer Kalyon presented on his company’s gigawatt-scale production base and included projections put together by Kalyon and other European upstream solar stakeholders on how a 5GW integrated solar manufacturing facility could come close to cost competitiveness with its Chinese counterparts.
Fath’s presentation detailed how a 5GW integrated facility, built at a cost of around €550 million (US$589.3 million), could produce modules at a cost of around US$0.227c/Wp, broadly competitive with a given cost in China of US$0.215c/Wp.
Critical to realising such a price is manufacturing at scale and with a vertically integrated supply chain in Europe, taking into account associated materials such as glass, EVA, aluminium and other components, reinforcing the notion that if Europe and other regions are to produce cost-competitive solar modules in the future, it’s not just a case of having cell or module assembly capacity.